Hydrogen Plants
Hydrogen Plants
Cotting Industries offers complete Hydrogen Gas Production Plants using its patented Double-Tube reformer or classic cylindrical reformer for hydrogen generation and Pressure Swing Adsorption for hydrogen purification. Double-Tube reformers and Pressure Swing Adsorption systems may be purchased separately.
Benefits
The pre-engineered hydrogen plant product line achieves superior economic performance by combining proven process technology with innovative component design and modular plant packaging. The product line allows hydrogen gas to be produced more reliably and cost effectively than any other small-scale hydrogen plant by:
- reducing capital investment;
- lowering operating cost;
- operating efficiently across a wide production range;
- setting new standards for safety and reliability;
- simplifying plant installation and operation;
- enabling low cost relocation to new sites; and
- providing for fully automated startup/shutdown, unattended operation and remote plant monitoring.
Additionally, the product line:
- eliminates availability concerns of compressed gaseous or cryogenic liquid hydrogen;
- provides an uninterrupted supply of hydrogen in regions with limited distribution infrastructure; and
- provides long-term hydrogen cost savings.
Features
The product line consists of seven plants with nominal capacities of 3,750 scfh, 7,500 scfh, 15,000 scfh, 35,000 scfh, 50,000 scfh, 70,000 scfh, and 85,000 scfh. Each plant incorporates the following unique design features:
- Compact, simple and efficient proprietary Double-Tube reformer or cylindrical reformer for hydrogen production.
- Fully integrated waste heat boiler for steam production.
- Feed gas desulfurizer for long catalyst life.
- Water-gas shift reactor for maximum hydrogen yield.
- Four-vessel pressure swing adsorption system for hydrogen purification.
- Factory installed process control system, instruments, light fixtures, and plug-and-play electrical wiring system for easy installation.
- Single point utility connections for convenient site tie-in.
- Automatic emergency shutdown system for maximum safety.
- 100% factory assembled on a portable steel skids for high quality, fast delivery and quick installation.
- Capable of processing multiple feedstocks including natural gas, biogas, propane, LPG, and naphtha.
- Designed to meet the codes and regulations required for installation in North America, Europe, China, Korea, and Japan.
Process Description
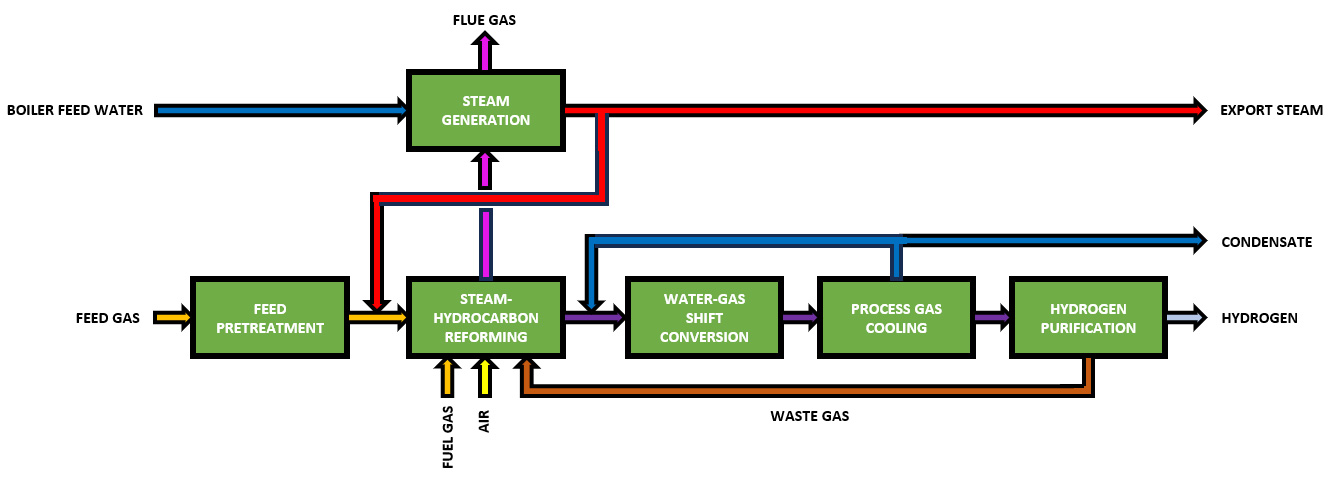
The process flow begins with a hydrocarbon feed gas entering the plant where it is preheated and sulfur compounds are removed via zinc oxide desulfurization. The sulfur free gas is mixed with saturated steam and further preheated before entering the reformer.
In the reformer, the steam/hydrocarbon mixture is converted to hydrogen and carbon monoxide at high temperature in the presence of a solid catalyst.
The hot reformed gas from the reformer is quenched with water and passed through the high temperature shift converter where steam and carbon monoxide are converted to additional hydrogen and carbon dioxide.
The process gas is cooled and then purified in the pressure swing adsorption system. Waste gas from the pressure swing adsorption system is burned as fuel in the reformer. The hot flue gas from the reformer is used to generate the steam required by the process and additional steam for export.